tomakichiコラム
どの辺で新品に変えた方がいい?
再研磨できる量(長手方向、径方向とも)は工具の種類、形状により異なります。
例えばドリルにおいては加工穴深さに対して径の2倍(φ10の穴なら20mm)以上の溝長が残っていないと切屑の排出性が悪くなり切屑づまりでドリル折損に繋がります。
エンドミルも外周刃を研磨して行けば溝の体積がどんどん狭くなり切屑排出性が悪くなり切屑を嚙み込んで加工面にキズが付いたり刃が欠けたりします。
加工内容により一概にここまで研磨できるとは言えません。が、短くなったり細くなった工具は別の加工に使って頂く事は出来ます。
また、工具の交換のタイミングは難しいですね。
再研磨するという前提で考えれば損傷が大きくなると除去する部分が多くなります。
傷みが激しければ先端から何ミリも切断追込みしなければならない場合もあります。
その際には切断費用も再研磨代に加算されてしまいますし、刃長が短くなり今までと同じ加工には使えなくなる事もあります。
一般的には大きな摩耗、大きな欠けが出ないうちに再研磨へ出すのが良いと思います。
ですが、製造現場のコストをどう見るかはその会社の経営者の判断によります。
コスト計算に正しい計算式はありません。
工具の損傷を犠牲にしても加工条件を上げて生産量を増やし納入先の希望納期を満足させて良いビジネス連携を強化する事も重要な事です。
また上記同様に加工条件を上げて残業や夜勤、休日出勤を行わず定時間内で作業を終了させる事で電力料や労務費を抑える事も経営方策のひとつ。
消耗品費と経費を天秤にかけてどちらが利益をより多く生み出すかの判断は経営者の考え方それぞれ。また仕事の入り方によって都度優先されるものは変わって来ます。
でも、一番良いのはリユース(再研磨)しかも最適スペックで生産性を上げて消耗品費と経費ともに削減する事。虫の良い話のようですが、これは再研磨であれば可能な事です。
再研磨の事例はこちらからご確認いただけます!
切削お役立ち情報NO.135です。前回と同じくプランジ加工の解説で、補足情報になります。
切削お役立ち情報NO.134です。プランジ加工は上手く加工にあてはまると、生産性が大きく改善されます。
切削お役立ち情報No.133 肩削り加工でのビビり対策となります。
切削お役立ち情報 No.132 今回も内径溝入れ時のビビり対策となります。
切削お役立ち情報 No.131 今回は内径溝⼊れ時のビビり対策となります。実際の加⼯事例が下記になります。
切削お役立ち情報 No.130 エンドミルの刃先には、刃先を強化する為にホーニングR(刃殺し)を施しています。 ホーニングRが0.1の場合、⼀刃の送り量を0.1㎜以上にする必要があります。 そうしない…
切削お役立ち情報 No.129 今回も前⽉の補⾜です。肩削り加⼯でのビビり改善の⽅法です。 不等ピッチの⼯具を使⽤するのも⼀つの⽅法となります。 吊り橋では、等間隔で渡ると振動が収まらず、共振が⼤きく…
切削お役立ち情報 No.128 今回は、前⽉の補⾜です。肩削り加⼯でのビビり改善の⽅法です。 切削抵抗を減らす為には、⼯具径を⼩さくするのも⼀つの⽅法となります。 ⼩径⼯具は、刃先とワークの接触⻑さが…
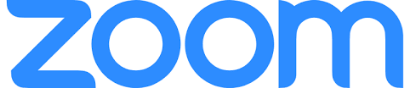

「日程の調整が難しい…」「来るのはちょっと…」というお客様もご安心ください!
tomakichiでは、zoomやGoogle MEETを用いた、オンライン相談も承っております!
※他のWeb会議システムにも対応可能です。
ご希望の方は、上記お問い合わせフォームの「オンライン商談を希望」にチェックを入れてください